Batteries
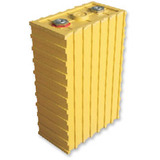

This section covers some of the more common battery chemistries you are likely to find powering electric vehicles.
Lithium Ion (LiIon)
Lithium batteries represent the most promising battery technology for electric vehicles. Similar to those used in laptops and mobile phones, lithium batteries are now available in large capacities for EV use. There are several lithium chemistries available. Lithium Polymer are typically the highest energy density but are prone to thermal runaway (catch fire) if damaged or overcharged. Lithium Iron Phosphate have somewhat lower energy density but are inherently more stable, and have very long cycle life, making them ideal for electric vehicle use.
|
![]() |
![]() |
||||||||||||||||
For more information, check out Wikipedia's article here: http://en.wikipedia.org/wiki/Lithium_Ion |
Lead Acid (PbA)
Lead Acid are the oldest type of rechargeable battery. They are very heavy for their energy and power, but are relatively cheap. Almost every petrol powered vehicle uses a lead acid battery for it's 12V power systems and starter motor. A lot of older EV conversions use lead acid due to their low cost, but for reasonable range a vehicle typically needs around one third of its total weight in batteries! (Such vehicles are sometimes known as "lead sleds".) We prefer to avoid lead acid batteries.
|
![]() |
![]() |
||||||||||||||||
For more information, check out Wikipedia's article here: http://en.wikipedia.org/wiki/Lead-acid_battery |
Nickel Metal Hydride (NiMH)
NiMH batteries had a promising start to use in EVs back in the mid to late 1990s. They offered a great improvement over lead acid which was, at the time, the only real alternative. There's actually an interesting story behind NiMH use in electric vehicles. NiMH batteries were developed by a company called Ovonics, in Michigan. They sold controlling interest in the technology to General Motors, who were interested to use them for their now-famous EV1 electric car. After the California Air Resources Board revoked their zero-emission mandate due to pressure from the automakers, GM sold the NiMH patents to Chevron Texaco, who formed the company Cobasys. Cobasys then sued Panasonic, who were making NiMH batteries for Toyota to use in their RAV4 Electric, forcing them to stop production of the vehicle. Since then, there have been no commercial electric vehicles powered by NiMH batteries. Click here to view an extract of the settlement. For more information (on NiMH batteries), check out Wikipedia's article here: http://en.wikipedia.org/wiki/Nickel_metal_hydride_battery |
![]() |
|
ZEBRA Battery
The ZEBRA battery was developed by an English company called Beta Research and Development (now owned by MES of Switzerland), and is a type of molten salt battery. These must operate at very high temperatures - around 300°C. As such they are usually an enclosed, insulated unit which includes a heater and battery management. This is only viable for large batteries (such as for EV applications), but it does yield rather good energy densities. Costs are significantly lower than Lithium, but at present power output is a lot lower. It's a technology that might be worth keeping an eye on - one day it may give Lithium a run for its money.
|
![]() |
![]() |
Battery Management Systems (BMS)
To maximise the life of batteries, it is recommended that all battery powered electric vehicles include a BMS, the purpose of which is to make sure the batteries remains within their ideal working parameters. Some battery chemistries (such as lead acid) are fairly tolerant of abuse, but all batteries benefit from having a BMS, and it will pay for itself with longer battery life. Lithium and NiMH both require a BMS for safety reasons, as they can be damaged if overcharged or overheated.
Some typical functions of battery management systems include:
- Charge balancing, to make sure all cells finish charging at the same time and to prevent damage through overcharging.
- Active balancing, where energy is diverted from stronger cells to weaker cells, to make sure all cells reach their maximum discharge point at the same time.
- Temperature monitoring, to avoid damage due to overheating. Some BMSes may also control a heater to bring cold batteries up to a better working temperature.
- Low-voltage cut-off, a means of isolating the battery pack when any cell reaches it's minimum recommended voltage, to avoid damage due to over-discharging.
- State-Of-Charge monitoring for all cells, through voltage and current monitoring the remaining capacity of each cell may be calculated.